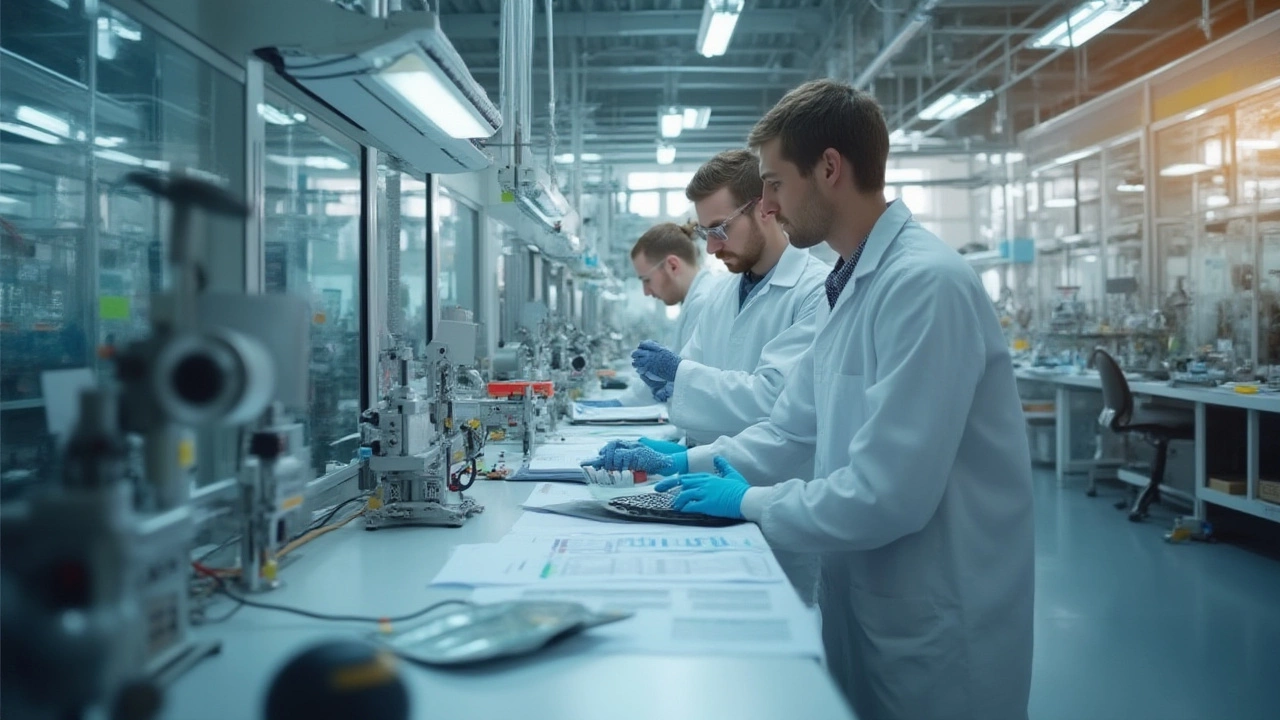
В 2023 году масштабный отзыв автомобилей знаменитой марки стоил компании почти миллиард долларов и подорвал доверие тысячи клиентов по всему миру. Всё из-за невыявленного дефекта детали, который на ранних этапах можно было бы устранить одним контрольно-измерительным инструментом и вниманием к процессу. Могли бы предотвратить катастрофу? Да. Как раз об этом – контроль качества. Жизнь бизнеса (а иногда и клиентов) напрямую зависит от того, насколько чётко выстроен этот процесс на каждом этапе производства. Некоторые ошибочно считают, что контроль качества — это про придирки и бесконечные проверки. На самом деле, это про предсказуемые результаты, отсутствие брака, снижение расходов и долгую, спокойную жизнь без громких скандалов.
Что такое контроль качества: суть и этапы процесса
Контроль качества — это система мероприятий, которая помогает определить, отвечает ли продукция или услуга установленным требованиям и стандартам. Не существует универсального рецепта: для разных отраслей набор процедур, инструментов и даже точек контроля может различаться. Но общий принцип всегда неизменен — контролеры должны обнаружить дефекты до того, как продукт попадет к клиенту. В 2022 году исследование Международной организации по стандартизации показало: ошибки, найденные по пути от сырья до склада готовой продукции, могут снизить производственные расходы вплоть до 24%. Интересно, что теперь во многих компаниях внедряют самоконтроль, где сами сотрудники отмечают замеченные дефекты, а не только сторонние инспекторы.
Все начинается с контроля входящего сырья. Здесь важно не пропустить некачественные материалы: 70% отказов оборудования и брака связано именно с сырьевыми ошибками. После этого идёт этап контроля технологических процессов. Например, на производстве подшипников обычная практика — проверка размерных параметров через каждые несколько сотен изделий. Дальше — контроль качества готовой продукции, который включает визуальный осмотр, разрушающие и неразрушающие испытания, а иногда и тестовую эксплуатацию. Стоит принять за норму: каждая партия продукции должна быть тщательно оценена, иначе риски дефектов только нарастают.
Распространённые этапы процедуры включают:
- Входной контроль (сырье, комплектующие)
- Промежуточный контроль (этапы производства)
- Финальный или приёмочный контроль (готовая продукция)
- Периодический контроль (на складе, при транспортировке)
Формируется и документация, фиксирующая обнаруженные несоответствия и решения по их устранению — без этого весь смысл процесса теряется. По статистике, компании, которые тщательно ведут журнал контроля качества, тратят на исправление ошибок в 2 раза меньше средств, чем там, где всё происходит "на глазок".
Этап контроля | Основная задача | Используемые методы |
---|---|---|
Входной | Не пропустить бракованное сырьё | Визуальный осмотр, анализ документации, лабораторное тестирование |
Промежуточный | Отследить и ликвидировать дефекты процесса | Шаблоны, калибры, онлайн-датчики, контрольные карты |
Финальный | Убедиться в качестве продукта перед отгрузкой | Тесты на надежность, визуальный осмотр, функциональные испытания |
Контроль качества работает не только в промышленности. Это фундамент и пищевой отрасли, и IT, и даже медицине. Но особенно критичен он там, где ошибка буквально стоит жизни — скажем, при сборке авиационных деталей. Пренебрегать нельзя.
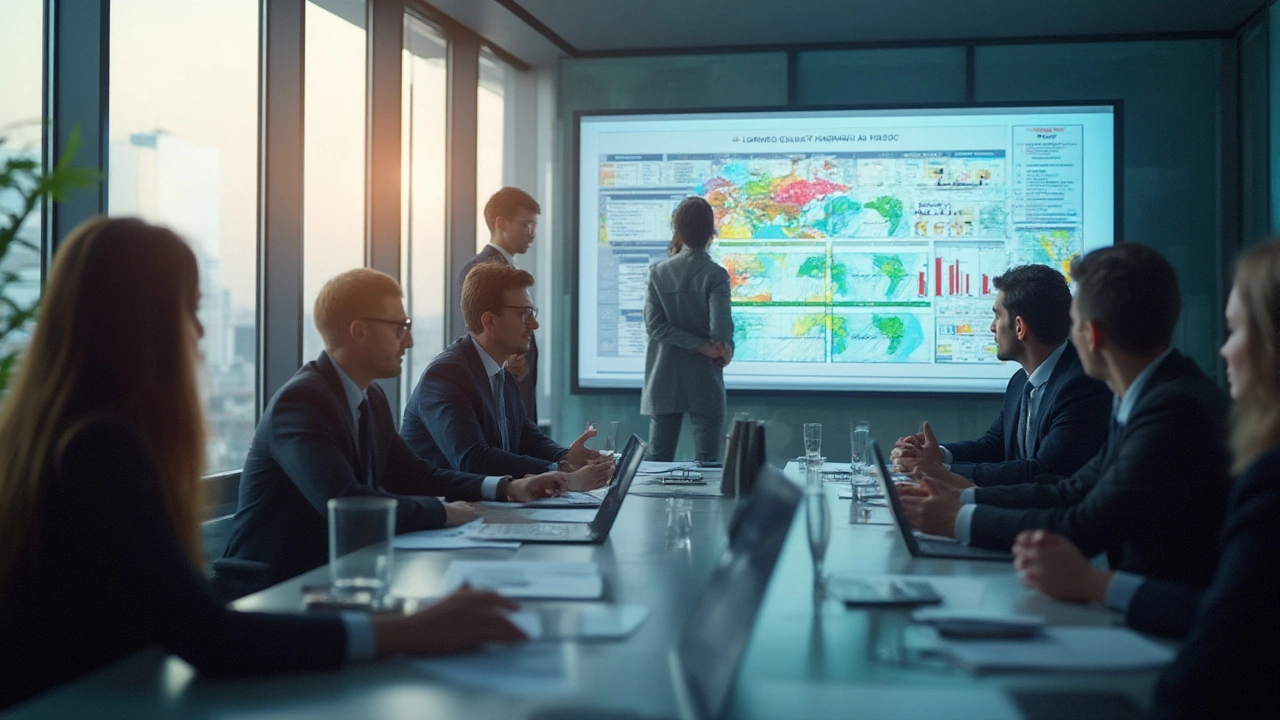
Методы и инструменты контроля качества: что реально работает?
Когда речь заходит о контроле качества, большинство сразу вспоминают линейки бюрократической рутины: галочки, акты, формуляры. Но по факту методы контроля намного шире, а часть из них реально помогает не допустить катастрофу, как в примере с массовым отзывом машин.
Есть простые способы — визуальный контроль, когда квалифицированный специалист буквально смотрит на изделие и отмечает дефекты. Такой путь актуален для товаров массового сегмента: коробки, этикетки, приборы. Но если нужна точность, применяют специальные измерительные приборы: микрометры, калибры, современные фотокамеры с искусственным интеллектом. В машиностроении и строительстве давно используют ультразвук для обнаружения пустот и внутреннего брака — и такие технологии сокращают вероятность пропущенного дефекта до 0,1%.
Отдельного внимания заслуживают статистические методы, например, контрольные карты Шухарта. Эти инструменты позволяют не только оценить, насколько соответствует партия товара стандарту, но и выявить нестабильные процессы ещё до критического сбоя. Например, внедрение контрольных карт на одном российском металлургическом комбинате позволило заранее узнать о малозаметных отклонениях в составе сплава и избежать миллионных потерь.
Среди методов, которые часто недооценивают, важное место занимают:
- Тестовые сборки и испытания
- Сенсорные системы и датчики для автоматического анализа
- Программное обеспечение для отслеживания несоответствий
- Инструменты обратной связи с клиентами после покупки
Современные технологии вытесняют ручной труд из контроля качества. Уже сейчас на крупных заводах работу инспекторов берет на себя искусственный интеллект: камеры и датчики самостоятельно анализируют качество пайки, цвет деталей, микротрещины. На Toyota действует правило «поймал ошибку – останови всю линию», и это работает: процент дефектных машин на выходе — меньше 0,2%. Интересно, что самые эффективные системы сочетают в себе и цифровые инструменты, и опытный человеческий взгляд. Ведь ни одна машина пока не отличает запах испорченного продукта или не чувствует подделку так, как это может сделать человек.
Для небольших предприятий ценным советом будет постепенное внедрение простых автоматизированных средств. К примеру, установка фотоэлементов и лазерных измерителей позволила одной арматурной компании из Екатеринбурга снизить выпуск брака с 6% до 2% за три месяца. Начинать стоит с самого уязвимого этапа: если больше всего ошибок появляется на сборке — туда и стоит направить максимум внимания.
Не забывайте и про обучение сотрудников. Часто именно нехватка квалификации становится причиной массового брака, особенно на небольших будущих производствах. Например, ежегодные практические тренинги на одном из автозаводов позволили сократить количество жалоб клиентов на 40%. А в IT-компаниях всё чаще применяют парное тестирование — когда двое специалистов совместно оценивают программные продукты, что значительно уменьшает число упущенных ошибок.
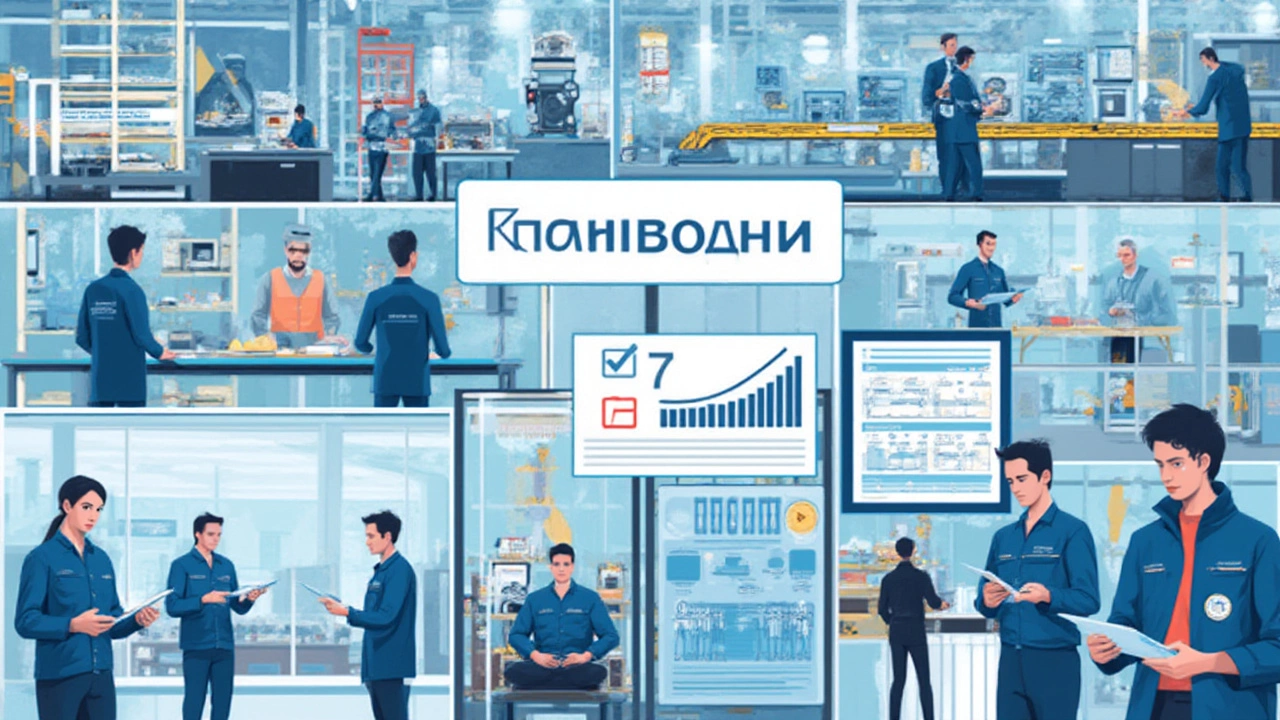
Современные вызовы и тренды контроля качества: взгляд в будущее
Сегодня требования к качеству растут невероятно быстро, причём не только из-за ужесточения стандартов, но и под давлением клиентов. Есть забавный факт: согласно опросу Gartner 2024 года, 79% покупателей готовы платить чуть больше за товар, если знают, что контроль качества на производстве построен без компромиссов. Логично — никто не хочет тратить деньги на подделки или услуги, которые не стоят своих денег.
Цифровизация меняет правила игры. Программы анализа больших данных фиксируют тенденции возникновения брака, зная точку сбоя до того, как она выльется в миллионную дилемму. Например, внедрение систем предиктивного анализа (Big Data) на одном из европейских автомобильных заводов снизило количество дефектных деталей почти на 25%. Неудивительно, что в последние 5 лет по всему миру открыли более 300 новых лабораторий по автоматизированному контролю качества. А искусственный интеллект на производстве в 2025 году становится уже не мечтой, а обыденностью.
Но цифровые решения — это не всё. Всё чаще на первый план выходит культура качества. На заводах внедряют программы поощрения за самые чёткие и своевременные обнаружения дефектов. Один японский производитель электроники раз в месяц вручает денежные призы инженерам, которые нашли даже малейшие отклонения, — и за год число серьёзных браков снизилось в 4 раза!
Большое значение приобрёл открытый обмен опытом между предприятиями. Компании всё чаще делятся методиками контроля, чтобы вместе бороться с контрафактом. Например, российский союз пищевых производств в 2024 году создал единую базу данных несоответствий, выявленных на складских этапах. Это позволяет быстро выявить проблемные партии по всей стране и не пустить брак на полки магазинов.
Тем, кто только делает первые шаги, пригодятся такие советы:
- Обеспечьте строгий входной контроль сырья. Помните — безопасность продукции начинается здесь.
- Не экономьте на обучении сотрудников. Совместная работа опытных и молодых специалистов — залог повышения культуры качества.
- Внедряйте цифровые средства постепенно — лучше хорошо контролировать одну зону, чем плохо все сразу.
- Ведите детальную статистику и анализируйте причины брака — это поможет не повторять одни и те же ошибки.
- Не бойтесь экспериментировать с новыми подходами и обсуждать их на отраслевых площадках.
Контроль качества не заканчивается на выходе из цеха. Лучшие производители проверяют продукт и спустя месяцы после продажи — собирают жалобы, анализируют поломки, корректируют техпроцессы. По-настоящему устойчивый бизнес строится не на тайном контроле, а на открытом внимании к деталям.
Контроль качества – это, по сути, пропуск на рынок, страховка от много миллионных убытков и залог того, что ваш бренд будут выбирать с уверенностью.