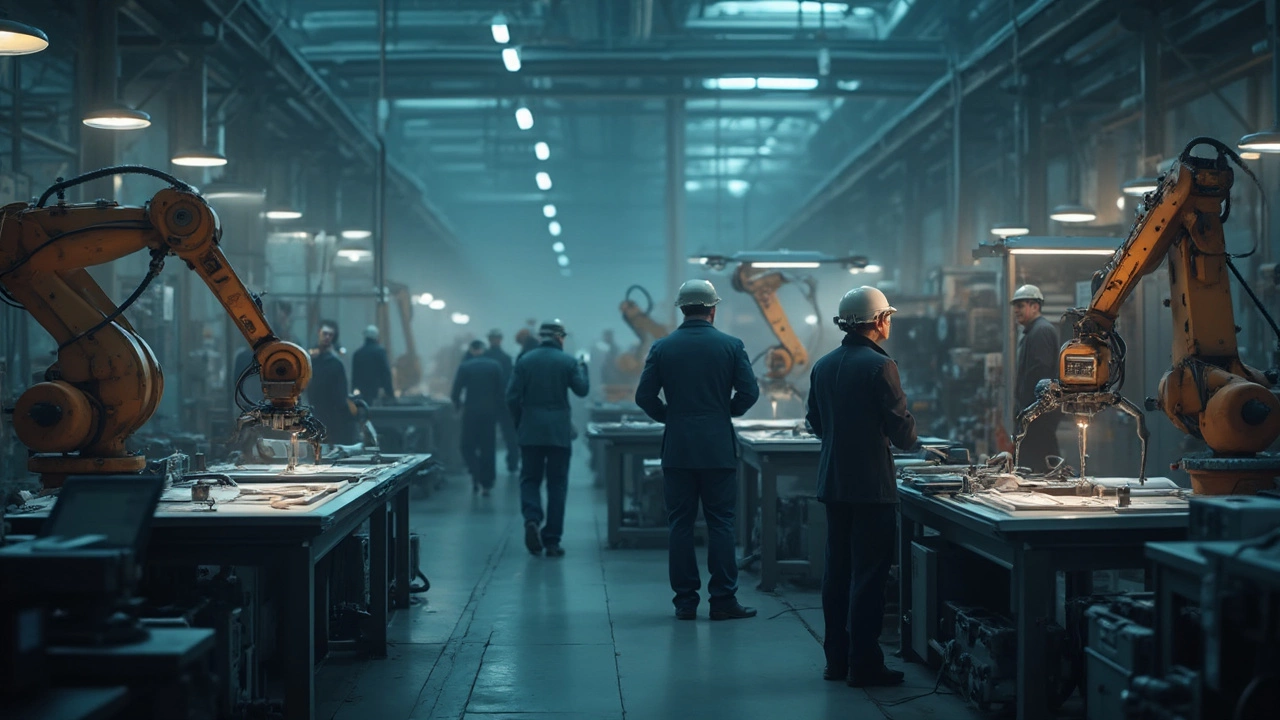
Зачем вообще говорить о проблемах в машиностроении? Просто игнорировать их не получится — если хоть одна «шестеренка» даст сбой, заводы теряют деньги, а клиенты получают не те детали, что были нужны. Да и случаи, когда некачественная деталь стоит компании миллионы, давно уже никого не удивляют.
Берём свежий пример: завод простаивает из-за поставщиков, сырья то нет, то оно приходит с браком. Знакомо? Такая история случилась с каждым, кто хоть раз запускал производство. И даже если все сделать идеально с точки зрения документации, без реального контроля за качеством ситуацию не исправишь.
Качество продукции напрямую зависит и от людей на линии, и от точности процессов, и от того, насколько вовремя замечают ошибку. Хороший начальник ОТК, грамотные операторы и поставщики, которые не срывают сроки — это уже половина успеха. Но только половина. Вторая часть — постоянный анализ, быстрая обратная связь и неустанная борьба за качество на каждом этапе.
- Главные трудности в отрасли
- Качество: почему сложно удержать планку
- Проблемы с кадрами: нехватка и подготовка
- Поставщики и материалы — неожиданные ловушки
- Цифровизация: как технологии влияют на качество
- Практические советы для повышения качества
Главные трудности в отрасли
Когда говорят о машиностроении, обычно сразу вспоминают проблемы с техникой — но всё куда шире. Сложнее всего даётся стабильное поддержание качества и организационные вопросы. Производство — процесс со множеством переменных, и контроль теряется на любом этапе.
За последние годы одна из самых наболевших тем — нехватка профессионалов. На заводах реально не хватает слесарей, токарей и инженеров с современными знаниями. Молодёжь идёт в IT, а бывшие опытные рабочие выходят на пенсию. Это сразу влияет на уровень брака и скорость выполнения заказов.
Вторая боль — сбои поставок. Российское машиностроение очень зависит от комплектующих и сырья. После известных событий 2022 года производителей буквально трясёт: запчасти то есть, то их ищут по всему СНГ или совсем не могут найти. В 2023 году по данным ассоциации «Станкоинструмент», каждый второй опрошенный завод сталкивался с простоями только из-за «сломанных» поставок.
Современные производства также мучаются с износом станков. Многие заводы до сих пор работают на оборудовании четвертьвековой давности. Когда ломается такой станок — найти детали, а главное, людей, кто починит, почти невозможно. Всё это снижает темп, тормозит развитие и приводит к непредвиденным расходам.
Ещё одна проблема — постоянная бюрократия и бумажная волокита. Любое изменение или переход на новое качество часто натыкается на согласования, старые инструкции, нежелание внедрять цифровые решения. Это съедает время и ограничивает модернизацию.
Актуальный факт: в опросе летом 2024 года заводы первых трёх регионов жаловались, что больше 30% времени уходит не на работу с деталями, а на согласование документов, переписку с надзорными органами и отчётность. Такие потери явно не добавляют производительности.
- Кадровый голод и старение специалистов
- Зависимость от поставщиков и логистических цепочек
- Старое оборудование и технические сбои
- Бюрократия и бумажная нагрузка
Каждый из этих пунктов напрямую сказывается на качестве продукции и конечных сроках выпуска. Только разобравшись с ними по отдельности, можно всерьёз сокращать брак и простои на предприятии.
Качество: почему сложно удержать планку
Вроде бы стандарты давно прописаны, техника есть, а качество в машиностроении всё равно часто оставляет желать лучшего. Почему? Здесь сложностей больше, чем кажется на первый взгляд.
На выходе ждут безупречные детали, которые выдерживают нагрузку, не ломаются и проходят проверку на каждом этапе. Для этого обычно созданы целые системы контроля и аттестации. Но на практике хватает нюансов:
- Разные партии материалов даже от одного поставщика могут отличаться по составу и свойствам. Это влияет на износ и надежность деталей.
- Оборудование изнашивается, точность настройки уходит — брак становится почти незаметным, пока он не попадает в окончательный продукт.
- Нагрузка на работников высокая, особенно на оператора у станка и контролёра качества. Один промах — и партия уходит с дефектом.
- Заводы вынуждены экономить, иногда жертвуя временем на контроль и обучение персонала.
- Из-за постоянных изменений заказов или сырья инструкции устаревают быстрее, чем их обновляют.
Примерно треть всех производственных дефектов появляется на этапе сборки и финальной обработки. Станки с ЧПУ тоже не всесильны: если задать неверную программу или «пропустить» износ инструмента, качество падает мгновенно.
А вот интересное: по данным Росстандарта, примерно 20% российских машиностроительных предприятий регулярно сталкиваются с возвратами из-за проблем с качеством. Вот небольшая сводка по частым видам брака:
Вид дефекта | Доля случаев (%) |
---|---|
Неточность размеров | 42 |
Поверхностные повреждения | 27 |
Использование неправильных материалов | 19 |
Ошибки сборки | 12 |
Если кажется, что всё просто, посмотрите на новую деталь на фоне тиража в 10 000 штук. И попробуйте не ошибиться. Самые продвинутые компании внедряют постоянный аудит процессов, чтобы ловить проблемы до того, как они дойдут до клиента. И это действительно работает, если менять подход системно, а не просто чекать бумажки ради галочки.
Реальные шаги для удержания качества включают регулярные проверки, диагностику станков, настройку сквозной системы контроля и участие всех сотрудников, а не только отдела ОТК. Всё на поверхности, но с «человеческим фактором» и тут не всегда справляются.
Проблемы с кадрами: нехватка и подготовка
В машиностроении острая нехватка специалистов — это факт, а не преувеличение. Если спросить директора большого завода, какая у него головная боль номер один, он чаще всего назовет дефицит квалифицированных рабочих и инженеров. Готовых кадров на рынке мало, а конкуренция за них высокая не только между заводами, но и с другими отраслями.
По данным ассоциации "Станкоинструмент", уже к 2024 году российская промышленность испытывала дефицит примерно в 250 тысяч технических специалистов. Причины понятны: молодежь редко выбирает профессии станочника или токаря, а многие учебные заведения не успевают обновлять программы. Старшее поколение выходит на пенсию, а новая смена не успевает прийти на замену — вот такая картинка по всей стране.
Чтобы не попасть в ловушку кадрового голода, компании идут на трюки:
- Перепрофилируют сотрудников под смежные задачи — токарь переучивается в наладчика оборудования.
- Инвестируют в свое обучение: создаются корпоративные курсы и партнерские программы с техникумами или вузами.
- Предлагают бонусы и быстрый карьерный рост молодым специалистам — иначе они уходят в IT или начинают работать по другой специальности.
Пример необычного подхода — компания «КамАЗ» организует стажировки прямо на заводах для студентов, и уже во время учёбы студенты получают приглашение на работу. Это порой оказывается эффективнее, чем просто размещать объявления на сайтах вакансий.
Вот как в реальности выглядит ситуация по нехватке персонала на крупных машиностроительных предприятиях:
Город | Процент вакансий в производстве, % | Основная проблема |
---|---|---|
Набережные Челны | 18 | Недостаток специалистов по ЧПУ |
Тула | 22 | Устаревшая система подготовки техников |
Екатеринбург | 15 | Массовый уход молодых кадров в IT |
Учить новичков с нуля — долго и затратно, но иногда это единственный выход. Машиностроение всегда выиграет, если будет на опережение работать с вузами и техникумами, внедрять менторство и давать шансы тем, у кого есть желание учиться. Тогда и качество продукции не подведет.
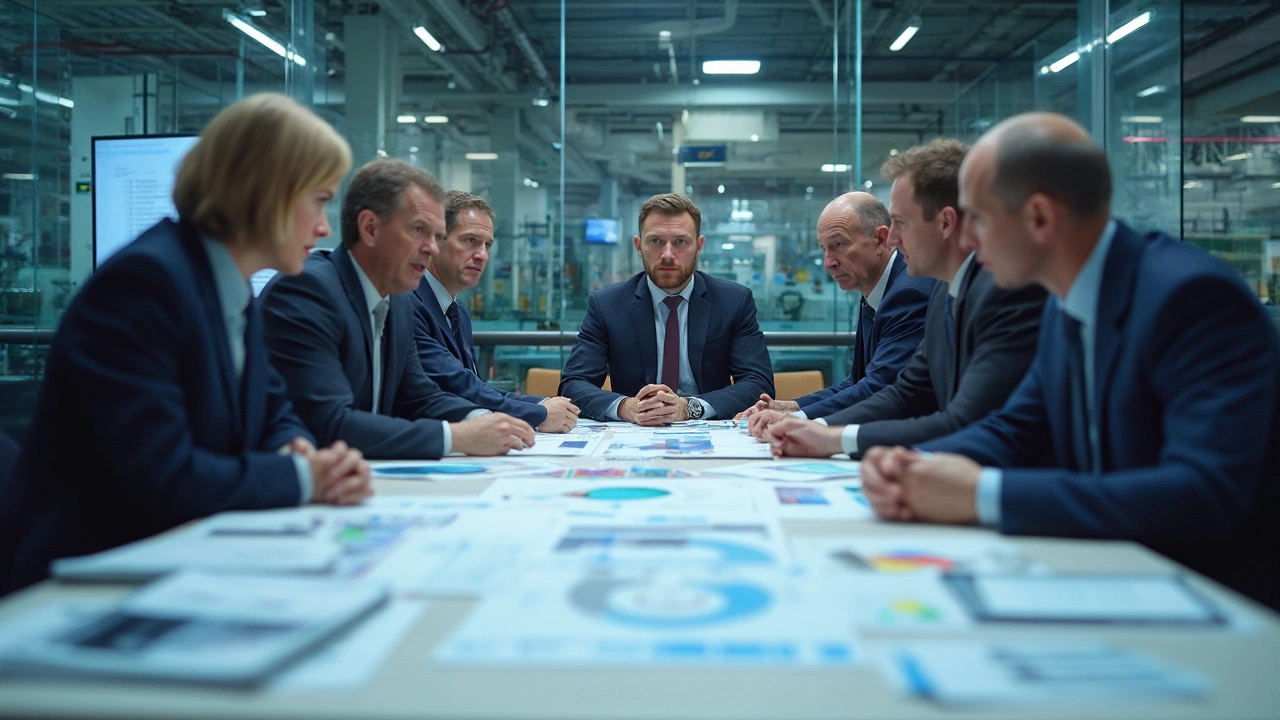
Поставщики и материалы — неожиданные ловушки
Не все проблемы в машиностроении рождаются «на месте». Иногда главная беда приходит вместе с сырьём или комплектующими. Представьте: приходит долгожданная партия деталей, а половина — с дефектами или совсем из другого материала. Это не редкость, а суровая реальность для заводов и цехов по всей стране.
Случается, что заводы зависят от одного-двух крупных поставщиков. Если хотя бы один подвёл, всё производство стопорится. Вот данные — по данным РАНХиГС на 2023 год, более 60% российских машиностроительных предприятий сталкивались с задержками и проблемами качества по вине сторонних поставщиков.
Частота проблем с поставщиками | Влияние на производство |
---|---|
60% предприятий | Задержки от 2 до 14 дней |
40% предприятий | Потеря 5–15% выручки из-за брака |
Часто речь идёт не только о задержках, но и о качестве материалов. Подмены марок стали, неправильные сертификации, брак в самой партии — получить «сюрприз» можно в любой момент. Один знакомый инженер рассказывал, как целую партию редукторов пришлось пустить на резку из-за «левого» алюминия в корпусе — так экономит поставщик, а расплачивается за это завод.
Так что можно сделать, чтобы не попадать в ловушки?
- Проверяйте каждую крупную партию — не ленитесь контролировать документы, сертификаты и реальные параметры материала, а не только бумажки.
- Не доверяйте одному поставщику — как только появляется альтернатива, проработайте запасные каналы поставки.
- Фиксируйте все претензии — заполняйте акты, делайте фото, не молчите даже по «мелочам», чтобы иметь на руках конкретику для разбирательств.
- Старайтесь заключать договоры с жёсткими пунктами про штрафы за срыв сроков и бракованное сырье.
Понятно, что заменить поставщика за день не получится. Но хотя бы подстраховаться реально. На крупных заводах есть даже отдельные отделы по работе с поставщиками, которые мониторят качество каждой поставки и ведут собственные рейтинги — это реально помогает вовремя выявлять проблемы ещё до того, как они ударят по всей цепочке.
Цифровизация: как технологии влияют на качество
В машиностроении цифра — не просто мода, а спасательный круг, особенно, когда речь идёт о качестве. Уже сейчас цеха внедряют системы цифрового мониторинга: датчики качества, автоматическую диагностику, даже виртуальные двойники для тестов оборудования. Всё это резко сокращает шансы брака.
По данным Ассоциации машиностроителей России, после внедрения цифровых решений количество дефектов упало почти на 30%. Например, автоматизированная система отслеживания и анализа дефектов на конвейере завода «КАМАЗ» сократила простои на линии буквально в разы.
Оцифровка помогает:
- моментально обнаружить сбой на раннем этапе, чтобы качество деталей не страдало;
- собрать честную статистику по частым ошибкам и понять, где «тонко»;
- отладить процесс так, чтобы человеческий фактор влиял меньше;
- сэкономить на ручных проверках — всё фиксирует цифровая система и сигналит, если что-то пошло не так.
Как сказал Сергей Бугаев, замдиректора по развитию цифровых технологий на одном из крупных предприятий:
«Раньше брак ловили глазами. Теперь — цифры сами укажут, где проблема и кто ответственен».
Но тут важно не просто поставить датчики ради галочки. Всё работает только когда эти системы реально интегрированы в процессы и есть команда, которая не игнорирует сигналы. Так что цифра сама по себе ничего не решит — нужен живой подход и контроль, чтобы качество было не только на бумаге.
Практические советы для повышения качества
Вряд ли кто-то спорит: если нет системы, качество в машиностроение будет страдать. Вот что реально работает на заводах, где ошибкам не дают шансов.
- Проверьте инструкции по сборке и контролю: делайте их максимально понятными, чтобы новый сотрудник мог разобраться без помощи соседа.
- Внедрите контрольные чек-листы: отмечать выполненные действия по пунктам правильнее, чем надеяться «на память».
- Регулярно обучайте команду: свежие знания — защита от повторяющихся ошибок. Фишка — перемешивать «теорию» и практику прямо на производстве.
- Ловите проблемы на самых ранних этапах: визуальные осмотры, замеры, тесты — всё идёт в дело. Так проще не допустить крупного брака.
Данные реального завода показывают: когда внедряется цифровая система контроля качества, количество претензий от заказчиков падает вдвое. И это не теория — в 2023 году на одном из тракторных заводов России после перехода на электронные протоколы брака число возвратов снизилось с 8% до 3,7% за полгода.
Год | Процент возвратов |
---|---|
2022 | 8% |
2023 | 3,7% |
А теперь еще пара советов из жизни:
- Обратная связь от людей у станка: уважайте замечания операторов — часто они первыми видят, где назревает проблема.
- Аудит поставщиков минимум раз в год: всё меняется, и вчерашний «надежный» вполне может расслабиться.
Заведите правило: если проблема повторилась — автоматический пересмотр процесса. Никто не застрахован, но упрощать и ждать самоисцеления — путь в тупик.
«Качество — это привычка, а не разовое усилие», — говорил Филипп Кросби, один из “отцов” современного управления качеством.
Вот и получается: шаг за шагом, день за днём — только так машиностроение выходит на новый уровень.