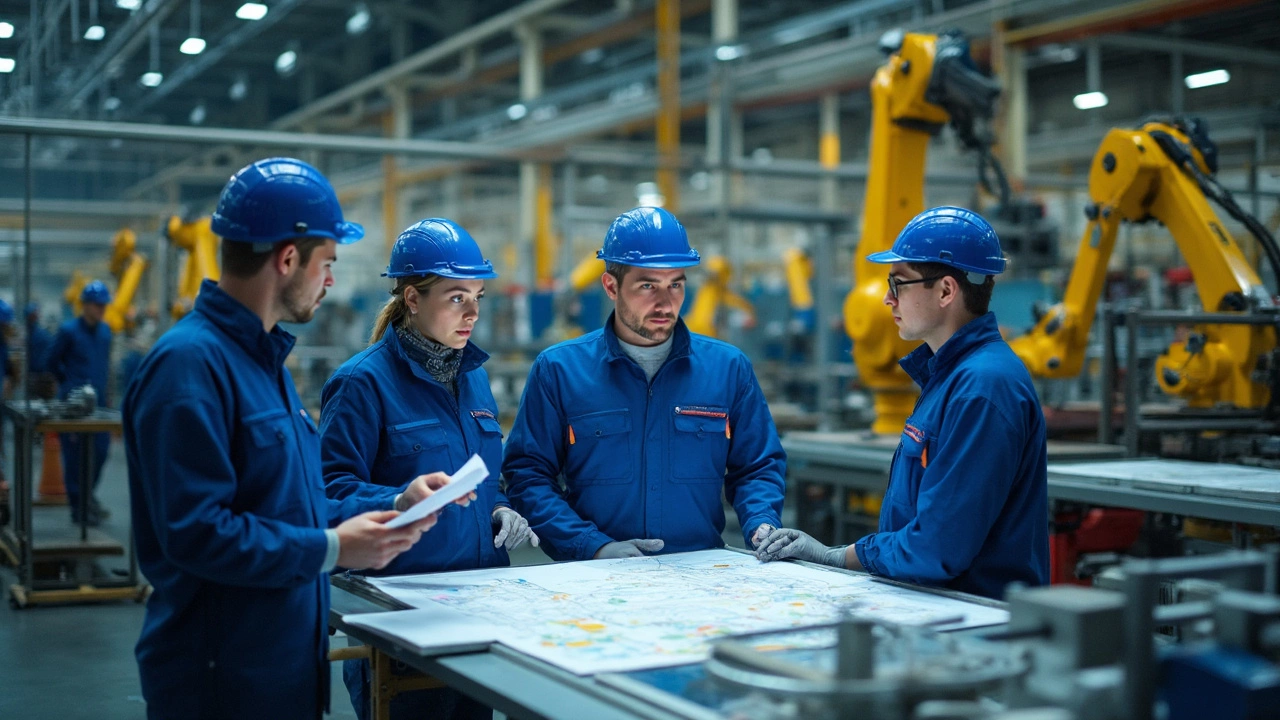
Контроль качества — не пустая формальность, особенно если речь о машиностроении. Тут ошибка на миллиметр может стоить не только денег, но и репутации, а иногда и жизни. Даже самая крутая деталь может дать сбой из-за крошечной трещины. Поэтому выбирать метод контроля — это не воля случая, а вопрос выживания бизнеса.
Сложно поверить, но в 2024 году на заводах ещё можно встретить дедовские методы — линейка, штангенциркуль. Для массового товара иногда и этого хватает, но если вы делаете не болты для забора, а сложные механизмы, тут уже другой разговор. Например, ультразвуковые и рентгеновские методы позволяют видеть то, что обычным глазом не поймёшь. Интересный факт: на одном питерском заводе ультразвуковой контроль выявил дефекты, которые обычный визуальный контроль пропускал годами — экономия на браке составила миллионы рублей в год.
Но не стоит бросаться в крайности. Перед покупкой дорогого оборудования стоит подумать: действительно ли нужен суперсовременный контроль или подойдут простые методы? Главное — не гнаться за модой, а реально оценивать свои задачи.
- Зачем нужен контроль качества именно в машиностроении
- Классические и современные методы контроля
- Как выбрать подходящий метод для конкретного производства
- Полезные советы: как не выкинуть деньги на ветер
Зачем нужен контроль качества именно в машиностроении
В машиностроении играют по-крупному: каждая ошибка в деталях может привести к остановке целого производства или, в худшем случае, поломке оборудования у клиента. Классика: не заметили микротрещину в шестерёнке — и уже через пару месяцев эта деталь развалилась в станке, который стоит миллионы.
Без строгого контроля качества рискуешь попасть на серьезные убытки: платить за ремонт, возвращать бракованную продукцию или разбираться с рекламациями. Вот почему даже мелкие заводы не могут позволить себе экономить на этом этапе.
Вот конкретные задачи, которые решает контроль качества на производстве:
- Снижение количества брака и потерь на переделке деталей.
- Стабильное выполнение ГОСТов и других стандартов — если детали не совпадают по размерам, ни один заказчик не примет партию.
- Защита репутации компании и долгосрочных контрактов с клиентами.
- Безопасность — у продукции для авто, авиации или энергетики требования предельно жёсткие.
Есть интересная статистика: по данным Ассоциации производителей РФ за 2023 год, из-за неэффективного контроля качества около 18% деталей для машиностроения в России возвращали на доработку. Это прямые потери времени и денег.
Проблема из-за плохого контроля | Потери |
---|---|
Возврат деталей | Вплоть до 10% выручки в крупных компаниях |
Срыв сроков поставки | Штрафы от заказчиков |
Ремонт оборудования у клиента | Дорогой сервис и потеря доверия |
Удивительно, но большинство брака появляется именно там, где контроль проводят вполглаза или экономят время на проверке. Поэтому тут нет мелочей: правильная система контроля качества — это не дополнительная трата, а страховка от серьезных провалов в будущем.
Классические и современные методы контроля
Если гуглить методы контроля в машиностроении, найдёте кучу вариантов — от поверки штангенциркулем до проверок при помощи сложных датчиков и ИИ. Давайте разложим всё по полочкам — что используют давно, а что пришло совсем недавно.
Классика — это визуальный и измерительный контроль качества. Его используют буквально все: проверяют размеры, посадки, геометрию. Это дешево и быстро, много здесь не надо: линейки, микрометры, калибры, иногда простые шаблоны. Полезно, если детали большие или простые по форме и требованиям к точности нет высоких.
Но если у вас детали сложные, тут уже нужны современные средства. Самые распространённые:
- Ультразвуковая дефектоскопия — обнаруживает внутренние трещины и пустоты. Эта штука реально спасает, когда сварные швы или толстый металл.
- Рентгеновский контроль — как в медицине, только для деталей. Можно обнаружить дефекты внутри корпуса, даже если всё снаружи суперровно.
- Магнитопорошковый контроль — ищет трещины у поверхности на магнитных деталях. Хорош для валов и крупных шестерней.
- Цифровое измерение (3D-сканеры и КИМ — координатно-измерительные машины) — загоняете данные в комп, быстро получаете отчёт. Это особенно круто, если детали идут мелкой серией или под нестандарт.
Есть и современные фишки. Например, автоматизация контроля на производстве. Если раньше всё измеряли вручную, то сейчас ставят датчики, которые идут по потоку и сами контролируют каждый этап. Это удобно, если выпуск большой партии и важна скорость. По данным Ассоциации производителей оборудования за 2023 год, внедрение цифровых КИМ увеличивает производительность инспекции деталей почти на 45% по сравнению с ручной проверкой.
Вот маленькая шпаргалка для сравнения:
Метод | Что ловит лучше всего | Скорость | Стоимость внедрения |
---|---|---|---|
Визуальный/измерительный | Геометрию, простые дефекты | Высокая | Низкая |
Ультразвуковой | Внутренние дефекты, металл, сварка | Средняя | Средняя |
Рентген | Сложные внутренние дефекты | Низкая | Высокая |
Цифровое измерение (КИМ) | Сложные формы, высокая точность | Высокая | Высокая |
При выборе метода в управлении качеством часто мешает соблазн попробовать что-то модное только ради галочки для аудита. Не поддавайтесь: главное не сияние технологий, а то, что реально снижает брак и экономит деньги.
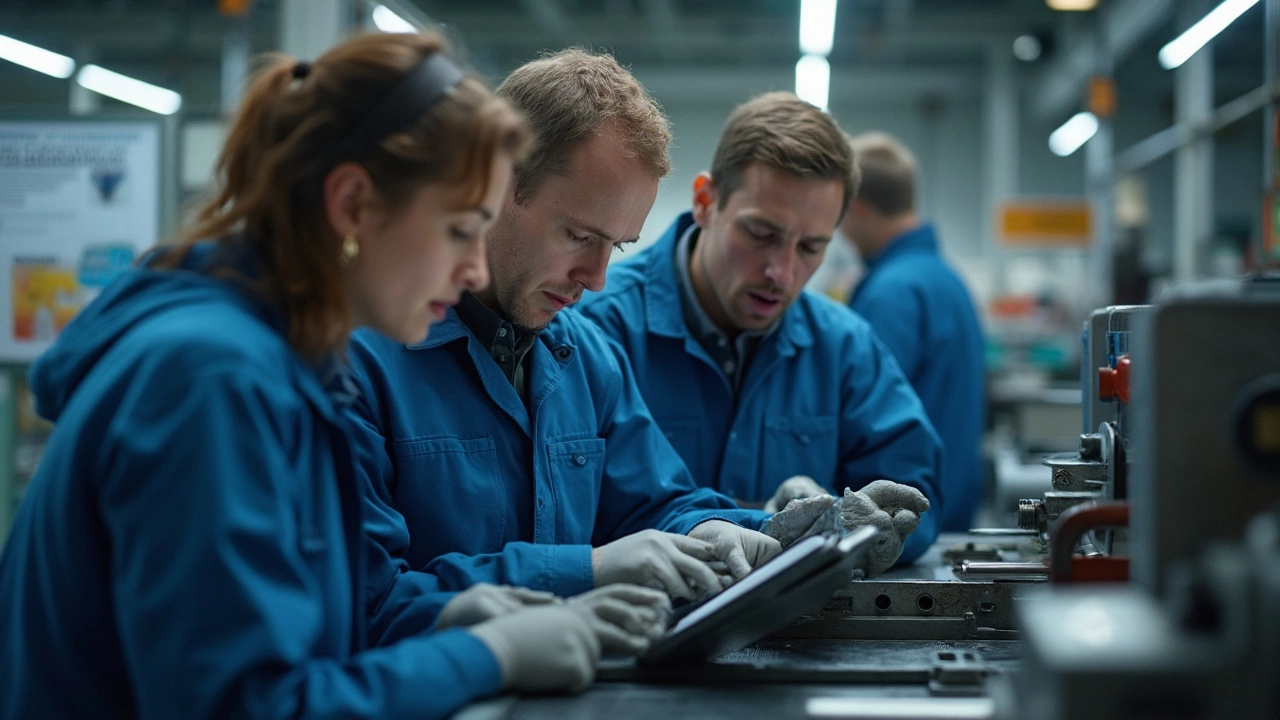
Как выбрать подходящий метод для конкретного производства
Не каждый метод контроля качества годится для любого цеха. Отличие в деталях, их размерах, материалах, требованиях к безопасности — и вот уже стандартный подход не катит. Сначала надо понять, что вы вообще производите: это массовое изделие, например гайки, или уникальные сложные детали, как корпуса редукторов?
Вот базовые вопросы, которые стоит задать себе перед выбором:
- Насколько высокая точность нужна? Для станков деталями с погрешностью даже в десятые доли миллиметра уже нельзя рисковать.
- Какой объем продукции ежедневно выходит с линии?
- Какие дефекты критичны: трещины, неправильная геометрия, внутренние пустоты?
- Готовы ли вкладываться в дорогое оборудование, например рентген или оптические измерители?
- Какие квалификации у сотрудников — смогут ли они пользоваться сложными системами?
Если речь о потоковом производстве, часто хватает автоматизированных линий с лазерными измерителями. Но если делать упор на уникальные крупные изделия или мелкосерийку, тут ручной и визуальный контроль качества иногда себя оправдывает, особенно когда нужно выявить внешний брак или дефекты типа сколов.
Полезный лайфхак: совмещать методы. Например, сначала визуальная проверка, потом ультразвук. Так можно не только повысить уровень управления качеством, но и сэкономить время — брак выбракуется на ранних этапах.
Метод | Подходит для | Вложения | Кадровые требования |
---|---|---|---|
Визуальный | Поверхностные дефекты | Минимальные | Базовые |
Ультразвуковой | Внутренние трещины | Средние | Специалист |
Рентгеновский | Скрытые дефекты, сложные детали | Высокие | Профессионал |
Лазерные системы | Массовое производство | Высокие | Обучение персонала |
Не забывайте про сертификацию. Если вы работаете под заказ на международный рынок, то стандарты ISO по управлению качеством могут dictate выбор методов. Иногда проще вложиться в обучение персонала под «чужие» стандарты, чем потом бороться с возвратами и штрафами.
Вот пример из жизни: на одном заводе решили перейти с ручного на ультразвуковой контроль качества — снизили количество брака на 30%, окупили прибор уже меньше чем за год. Цифры говорят сами за себя.
Полезные советы: как не выкинуть деньги на ветер
Покупать дорогое оборудование для контроля качества хочется, особенно когда менеджеры поставщиков обещают «революцию» в цехе. Но практика другая: половина таких закупок через год просто пылится на складе. Чтобы не попасться, держу вот такой чек-лист:
- Без четких задач никакой метод не поможет. Сначала разберитесь, зачем вам этот контроль: вы хотите сократить брак или нужно повысить доверие заказчика?
- Тестируйте наработки на малых партиях. Не вкладывайтесь сразу в полный цикл — попробуйте метод на отдельной линии или группе деталей.
- Сравните стоимость ручного и автоматизированного контроля. Иногда человек с опытом выявит проблемы быстрее и дешевле камеры за миллион рублей.
- Обратите внимание на возврат инвестиций — сколько реально окупится потраченных средств? Например, если ваш брак выше среднего по отрасли (например, более 4% по данным Минпромторга РФ за 2023 год), внедрение автоматизированного контроля часто окупается за 1-2 года, но если у вас и так всё чётко — вложения будут лишними.
- Не верьте голому маркетингу. Просите реальные кейсы с похожими масштабами производства. Сравните отзывы от других заводов, особенно если они из вашего региона — это часто лучшая реклама или антиреклама.
Для понимания, как может выглядеть реальная экономия, вот пример:
Метод контроля | Инвестиции, руб | Снижение брака | Окупаемость (мес) |
---|---|---|---|
Визуальный контроль | 100 000 | 5% | Быстро (3-6) |
Ультразвуковой | 1 500 000 | 20% | 12-18 |
Автоматизированные камеры | 5 000 000 | 30% | 18-24 |
Еще совет: выделяйте средства не только на сам прибор или систему контроля, но и на обучение сотрудников. Куча заводов теряли деньги только потому, что люди не понимали, как пользоваться новым оборудованием — ошибку не заметили, проблему не выявили.
И, конечно, не забывайте о сервисе — регулярное обслуживание оборудования для управления качеством в машиностроении часто стоит меньше, чем устранение серьёзной аварии или расследование бракованной партии.